Management Approach
Brady's commitment to be a sustainable company is rooted in two important areas: reducing our overall environmental footprint and continuously improving our safety performance. In 2010, we conducted a materiality assessment which helped us identify and prioritize the sustainability issues most relevant to our business. These became the four focus areas of our "Sustainable Company Pillar." They are: eliminate waste, conserve energy and reduce greenhouse gas (GHG) emissions, preserve natural resources, and continuously improve safety performance.
Within each of these focus areas we have developed targets and Key Performance Indicators (KPIs) which are used to assess performance at each Brady facility and which have become part of our ongoing operational reviews. We recognize the business value of continually tracking and transparently reporting on these metrics. KPIs are collected monthly at the site level, reviewed quarterly by the Sustainable Company Council led by the global VP of Operations and reviewed annually by the Sustainability Steering Team. Tracking and monitoring our facility data more closely has enabled us to better understand our sustainability impacts, identify areas for improvement and enhance business decision-making.
Throughout 2012, the Green Team planned and implemented several initiatives focused on waste reduction, employee wellness, and enhancing overall employee awareness of sustainability issues. In 2013, the Green Team will continue to roll out the successful model it has created in Milwaukee at other locations across North America.
In our inaugural sustainability report published last year, we established 2011 as our official baseline of performance which will be used to measure future year-over-year improvement. This update will cover environmental and safety sustainability performance information for Calendar years 2011 and 2012.
In order to improve the accuracy and consistency of our data collection methods, we implemented operational improvements for our enterprise-wide data collection system to help us better manage our facility data. With new systems in place to drive continuous improvement, including independent reviews conducted by our internal audit team, we are confident in the accuracy of the data presented in this report.
Brady also has a number of policies that guide us in our commitment to having a sustainable company. Our Environmental and Safety Policy has been in place since 1998, and we added a Critical Program Elements (CPE) Environment & Safety Management System in 1999 to ensure monitoring and review of our environmental and safety performance on a regular basis. In 2011, we established a formal Sustainability Policy.
Training and Awareness
All Brady facilities have developed environmental training programs to educate employees about the global Environmental and Safety Policy, environmental impacts of the business, and employees' individual roles and responsibilities for the CPE E&S management system.
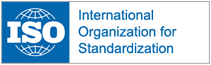
In addition, we are building off of our CPE E&S management system to attain certification to the ISO 14001 standard at our largest facilities. To date, we have achieved certification at 14 Brady facilities as follows:
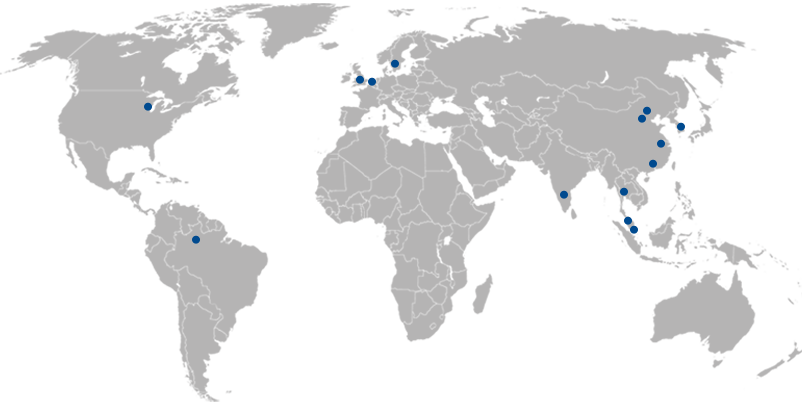
- Zele, Belgium
- Manaus, Brazil
- Beijing, China
- Langfang, China
- Wuxi, China
- Shenzhen, China
- Bangalore, India
- Penang, Malaysia
- Gumi, South Korea
- Nödinge, Sweden
- Singapore
- Rangsit, Thailand
- Stockport, UK
- Milwaukee, US
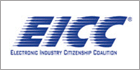
In 2011, we also agreed to abide by the Electronic Industry Citizen Coalition (EICC) Code of Conduct at 18 facilities in 12 different countries and began formally reporting on our performance against the code for these sites to select customers. The aim of the Code is to improve efficiency and social, ethical and environmental responsibility in the global supply chain. The Code of Conduct covers five critical areas of sustainability performance: labor, health and safety, environment, management systems, and ethics.
Teamwork
Teamwork is a core value at Brady and is exhibited in many ways daily. A number of team activities are also focused on sustainability. These include:
- Brady's Green Team (Americas)
Brady's inaugural Green Team was formed in early 2011 at the company's headquarters in Milwaukee, Wisconsin. The employee-driven group works to define, deploy and drive sustainability activities, initiatives and projects in our businesses in order to bring Brady's sustainability strategy to life through day-to-day, practical actions. Throughout 2011 the Green Team planned and implemented several initiatives focused on waste reduction, employee wellness, and enhancing overall employee awareness of sustainability issues. The Green Team aims to roll out the successful model it has created in Milwaukee in the form of a playbook to guide Green Teams at Brady facilities in other regions in 2012 and 2013. - In 2012, the Green Team worked with business management to identify and assign leaders for Green Teams at each of our major manufacturing locations, which will be included in the planning and execution of environmental improvement programs in 2013. The Green Team leaders meet quarterly and consults with their colleagues in different regions to identify challenges and solicit ideas for new environmental initiatives. They will host their first multi-plant meeting in mid-2013 and are developing a database for sharing ideas, data and information, promotional materials, and guidelines for the replication of successful projects.
- Treasure Hunt and Kaizan Events (Global)
Employees at Brady facilities around the world participate in "treasure hunt" and Kaizen events to identify waste and energy and GHG emission reduction opportunities. Each suggestion for improvement is evaluated and prioritized based on the impact on the business and the relative ease of implementation, and plans developed to roll out individual changes at each facility. - Brady continued to realize cost savings from treasure hunts and other sustainability initiatives, adding approximately another $276,000.